Essential Soldering Iron Safety Practices
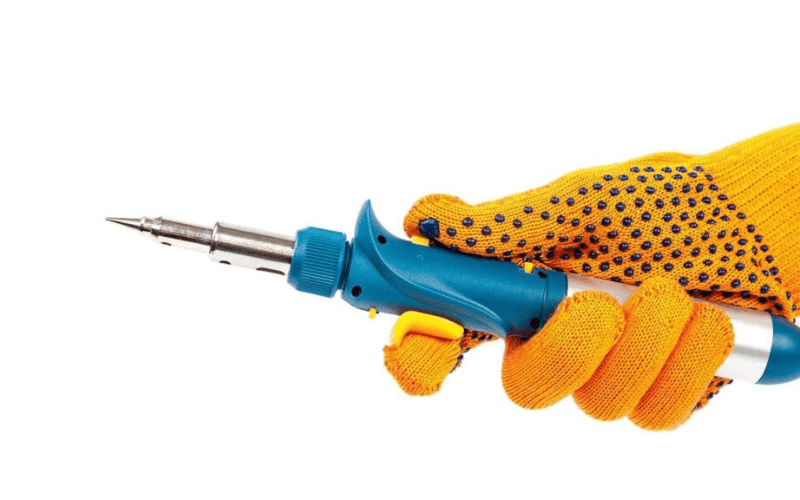
Introduction
Welcome to our comprehensive guide on soldering iron safety practices. In this article, we will explore the importance of adhering to safety guidelines, using personal protective equipment (PPE), and implementing best practices for ensuring a secure working environment when operating soldering irons. Whether you are a professional or a hobbyist, it is crucial to prioritize safety to minimize the risk of injury and property damage. Let’s delve into the essential safety measures for soldering iron operations.
Understanding Soldering Irons
What is a soldering iron?
A soldering iron is a hand tool used in soldering. It supplies heat to melt solder, which is used to join two or more pieces of metal together. In essence, a soldering iron is the primary tool in the process of soldering, making it an indispensable device for electronics assembly, metalwork, and various DIY projects.
- Heating Element: Generates the necessary heat for melting solder.
- Tip: The part of the soldering iron that comes into direct contact with the components being soldered.
- Handle: Provides a comfortable grip and insulation from the heat of the iron.
Types of soldering irons
When it comes to soldering irons, there are several types available, each with its own unique features and applications. Here’s a detailed look at the main types of soldering irons:
- Standard Soldering Iron: This is the most common type of soldering iron. It consists of a heated metal tip and a handle. It’s suitable for general purpose soldering tasks and is widely used in electronics, jewelry making, and small DIY projects.
- Soldering Station: A soldering station combines a soldering iron with a variable power supply and temperature control. It provides more precision and control, making it ideal for professional soldering work, circuit board assembly, and intricate soldering tasks.
- Butane Soldering Iron: This type of soldering iron is powered by butane gas, offering portability and versatility. It’s commonly used for field repairs, outdoor soldering, and situations where electrical outlets are not available.
- Soldering Gun: The soldering gun, also known as a pistol-grip soldering iron, is designed for high-power applications, such as heavy-duty soldering on large electrical connections, wires, and stained glass projects.
Importance of soldering iron safety
Soldering iron safety is of utmost importance when working on electronic projects or any soldering-related tasks. Accidents involving soldering irons can result in serious injuries and damage to equipment. It is crucial to adhere to safety guidelines and best practices to ensure a safe and efficient soldering experience.
- Personal Protection: When using a soldering iron, it is essential to wear protective gear such as safety glasses, heat-resistant gloves, and a long-sleeved shirt to prevent burns and other injuries.
- Workspace Safety: Maintain a clean and organized workspace to minimize the risk of accidents. Avoid placing flammable materials near the soldering area and use a fire-resistant work surface.
- Proper Ventilation: Soldering produces fumes that can be harmful when inhaled. Ensure adequate ventilation in the work area, and if possible, use a fume extractor to remove harmful fumes and gases.
- Temperature Control: Always use the soldering iron at the recommended temperature settings. Operating at excessively high temperatures can cause damage to components and increase the risk of accidents.
- Safe Handling and Storage: After use, allow the soldering iron to cool down before storing it in a secure and designated location. Proper handling and storage minimize the risk of accidental burns and damage.
Safety Precautions Before Soldering
Selecting the right soldering iron
When it comes to choosing the right soldering iron for your projects, there are several key factors to consider. Selecting the appropriate soldering iron can significantly impact the quality of your work and your overall experience. Here are some essential points to keep in mind:
- Wattage: The wattage of the soldering iron determines its ability to generate heat. For general electronics work, a soldering iron with 20-40 watts is suitable, while larger projects may require 40-80 watts.
- Temperature Control: Opt for a soldering iron that offers temperature control features. This allows you to adjust the heat based on the specific requirements of different components and materials.
- Tip Variety: Different soldering tasks may require different tip shapes and sizes. Choose a soldering iron that provides a variety of interchangeable tips to accommodate various soldering needs.
- Quality and Durability: Invest in a soldering iron that is well-built and durable. Look for models with heat-resistant handles, high-quality heating elements, and replaceable parts to ensure longevity.
By carefully evaluating these factors and selecting the right soldering iron, you can enhance the precision, efficiency, and overall success of your soldering projects.
Inspecting the soldering iron
Inspecting the soldering iron is a critical step to ensure its safety and effectiveness. Here are some key aspects to consider:
- Tip Condition: Check the condition of the soldering iron tip. Look for any signs of corrosion, wear, or damage. A damaged or worn-out tip can lead to poor solder joints.
- Heating Element: Examine the heating element for any visible damage or signs of overheating. A damaged heating element can result in inconsistent temperature and performance.
- Power Cord: Carefully inspect the power cord for any fraying, exposed wires, or damage. A frayed cord can pose a safety hazard and should be replaced immediately.
- Stand: Ensure that the soldering iron stand is stable and in good condition. A reliable stand is essential for safe and convenient placement of the iron during work.
- Temperature Control: If the soldering iron has temperature control features, verify that it is functioning properly. Test the temperature settings to ensure accurate and consistent heat delivery.
Preparing the work area
Before you start soldering, it’s important to prepare your work area to ensure safety and efficiency. Here are some essential steps to take when preparing the work area:
- Clean the Work Surface: Clear the work surface of any clutter, debris, or flammable materials. A clean and organized work area reduces the risk of accidents and helps you focus on the task at hand.
- Use a Heat-Resistant Mat: Place a heat-resistant mat or an insulating material on the work surface to protect it from heat damage. This will also provide a stable and safe surface for soldering.
- Ensure Adequate Ventilation: Soldering can produce fumes that may be hazardous if inhaled. Work in a well-ventilated area or use a fume extractor to minimize exposure to soldering fumes.
- Organize Tools and Materials: Arrange your soldering tools, solder, and components in a neat and accessible manner. This helps streamline the soldering process and reduces the likelihood of misplacing essential items.
- Secure Loose Cables and Wires: Ensure that cables, wires, and cords are not tangled or dangling. Secure them in place to prevent accidental tugging or tripping during soldering.
Safety Practices During Soldering
Using personal protective equipment
When soldering, it’s crucial to prioritize your safety by using the appropriate personal protective equipment (PPE). Here’s a detailed look at the essential PPE for soldering:
- Safety Glasses: Protect your eyes from any solder splashes, fumes, or accidental contact with the soldering iron.
- Heat-Resistant Gloves: Shield your hands from burns and other heat-related injuries.
- Respiratory Mask: Filter out harmful fumes and particles from the soldering process, ensuring you breathe clean air.
Furthermore, it’s essential to select PPE that fits well, is comfortable to wear, and does not hinder your ability to work safely and effectively. Ensure that all PPE is in good condition and replace any damaged or worn-out items.
Handling the soldering iron safely
When working with a soldering iron, it is crucial to follow specific safety measures to prevent accidents and injuries. Here are some detailed guidelines on handling the soldering iron safely:
- Use the right soldering iron: Ensure that the wattage and tip size of the soldering iron are suitable for the task at hand. Using the wrong soldering iron can lead to poor solder joints or overheating, posing a safety risk.
- Inspect the soldering iron: Before each use, check the soldering iron for any signs of damage, frayed cords, or loose connections. A well-maintained soldering iron reduces the risk of electrical hazards.
- Handle with care: Always hold the soldering iron by the insulated handle, and never touch the metal parts directly. This prevents accidental burns and ensures safe operation.
- Use a suitable stand: When not in use, place the soldering iron on a heat-resistant stand to prevent it from causing fires or coming into contact with flammable materials.
- Power off and unplug: After completing the soldering work, turn off the soldering iron and unplug it from the power source. Allow it to cool down before storing it in a safe location.
Dealing with solder fumes
When soldering, it is important to address the issue of solder fumes to ensure a safe and healthy working environment. Solder fumes are created when flux in the solder is heated and vaporizes, releasing potentially harmful gases and particles into the air.
Here are some key points to consider when dealing with solder fumes:
- Ventilation: Ensure proper ventilation in the soldering area to effectively remove fumes. This can be achieved through the use of fume extractors, local exhaust systems, or working in well-ventilated spaces.
- Use of Fume Extractors: Consider using fume extractors with activated carbon filters to capture and remove harmful fumes from the air.
- Personal Protective Equipment: Wear appropriate personal protective equipment such as respirators, masks, or goggles to minimize inhalation of fumes and exposure to flux particles.
- Workstation Setup: Position the soldering station in a way that minimizes the exposure of other individuals to solder fumes. Utilize protective barriers or enclosures when necessary.
- Regular Breaks: Take regular breaks to allow for fresh air circulation and reduce prolonged exposure to solder fumes.
By implementing these practices, soldering professionals can effectively manage and minimize the risks associated with solder fumes, promoting a safer and healthier working environment.
Preventing burns and injuries
When working with a soldering iron, it’s crucial to take measures to prevent burns and injuries. Here are some important guidelines to follow:
- Use heat-resistant gloves: Always wear heat-resistant gloves when handling the soldering iron and working with hot components. This will protect your hands from accidental burns.
- Keep a first aid kit nearby: Make sure a first aid kit is easily accessible in case of burns or injuries. Immediate treatment can prevent further complications.
- Proper workspace organization: Keep the soldering area well-organized and free from clutter to reduce the risk of accidental burns or injuries.
- Be mindful of hot surfaces: Avoid touching hot surfaces of the soldering iron or other equipment. Use designated holders and stands to place the soldering iron when not in use.
- Knowledge of emergency procedures: Educate yourself and others in the workspace about the appropriate emergency procedures in case of burns or injuries.
Emergency Procedures
Dealing with burns and injuries
When dealing with burns and injuries in the workshop, it’s important to take immediate action to address the situation. Here are some key steps to follow:
- Assess the severity of the burn or injury. Minor burns and injuries can usually be treated with basic first aid, while more serious cases require immediate professional medical attention.
- If the skin is burned, run cool water over the area for at least 10 minutes to reduce the risk of further damage and alleviate pain.
- Cover the burn or injury with a sterile, non-adhesive dressing to protect it from infection and further trauma.
- For minor burns, apply an antibiotic ointment and cover with a clean bandage. Seek medical attention for more severe burns.
- Keep an eye on the injured person for any signs of shock, such as rapid pulse, shallow breathing, or pale skin. If shock is suspected, seek immediate medical help.
It’s also essential to prevent burns and injuries in the first place by taking necessary safety precautions, using protective equipment, and following best practices for handling tools and equipment.
Workshops and manufacturing environments are prone to certain common injuries, including:
- Cuts and lacerations from sharp tools or machinery
- Eye injuries from flying debris or exposure to harmful substances
- Sprains and strains from lifting or carrying heavy objects
- Burns from hot surfaces, chemicals, or soldering equipment
- Electric shock from faulty equipment or improper handling
By being aware of these potential risks and taking appropriate safety measures, it’s possible to minimize the occurrence of burns and injuries in the workshop. Training employees on proper safety protocols, providing necessary protective gear, and maintaining a clean, organized workspace are all crucial steps in creating a safe working environment.
Addressing soldering iron malfunctions
As a crucial tool in electronics and metalworking, the soldering iron is prone to various malfunctions that can hinder its performance. By understanding common issues and their remedies, you can ensure the efficient operation of your soldering iron.
Here are some typical malfunctions encountered with soldering irons:
- Tip Oxidation: When the tip of the soldering iron becomes oxidized, it can lead to poor heat conduction and solder adhesion. This often occurs when the iron is left idle for an extended period.
- Temperature Regulation: Inaccurate temperature control can result in overheating, damaging components, or insufficient heat, leading to weak solder joints.
- Heating Element Failure: The heating element may degrade over time, causing inconsistent heat distribution and eventual failure.
- Poor Solder Flow: Issues with solder flow can stem from contaminated tips, improper soldering techniques, or faulty solder wire.
Here are some prevalent malfunctions encountered with soldering irons:
- Tip Oxidation: When the soldering iron tip undergoes oxidation, it can lead to subpar heat conduction and solder adhesion. This often arises from prolonged periods of inactivity.
- Temperature Regulation: Inaccurate temperature control can result in overheating, potentially damaging components, or inadequate heat, leading to weak solder joints.
- Heating Element Failure: Over time, the heating element may deteriorate, causing inconsistent heat distribution and eventual malfunction.
- Poor Solder Flow: Issues with solder flow can stem from contaminated tips, improper soldering techniques, or defective solder wire.
To effectively address these malfunctions and maintain optimal soldering performance, consider the following approaches:
- Cleaning and Tinning: Regularly cleaning the soldering iron tip and applying fresh solder can prevent oxidation and improve heat transfer.
- Calibrating Temperature: Employ a reliable temperature control system to ensure precise and consistent heat levels for various soldering tasks.
- Regular Maintenance: Conduct routine inspections on the heating element and replace it as needed. Additionally, prioritize proper ventilation to extend the lifespan of the soldering iron.
- Enhancing Soldering Technique: Practice appropriate soldering methods, including using the correct amount of flux and ensuring adequate solder flow, to achieve high-quality solder joints.
Conclusion
As we conclude our exploration of soldering iron safety practices, it is evident that prioritizing safety measures is indispensable for minimizing the risk of accidents and ensuring a secure working environment. By adhering to safety precautions, using personal protective equipment, and implementing best practices during soldering operations, individuals can safeguard themselves and others from potential hazards associated with soldering irons. Whether engaged in professional soldering tasks or pursuing hobbyist projects, the implementation of comprehensive safety measures is crucial for promoting a safe and secure workspace.